在现代材料科学和工程领域,对材料在高温环境下的摩擦磨损性能研究至关重要。高温摩擦磨损试验机应运而生,成为科研人员手中不可或缺的关键设备,为众多行业的发展提供了有力支持。
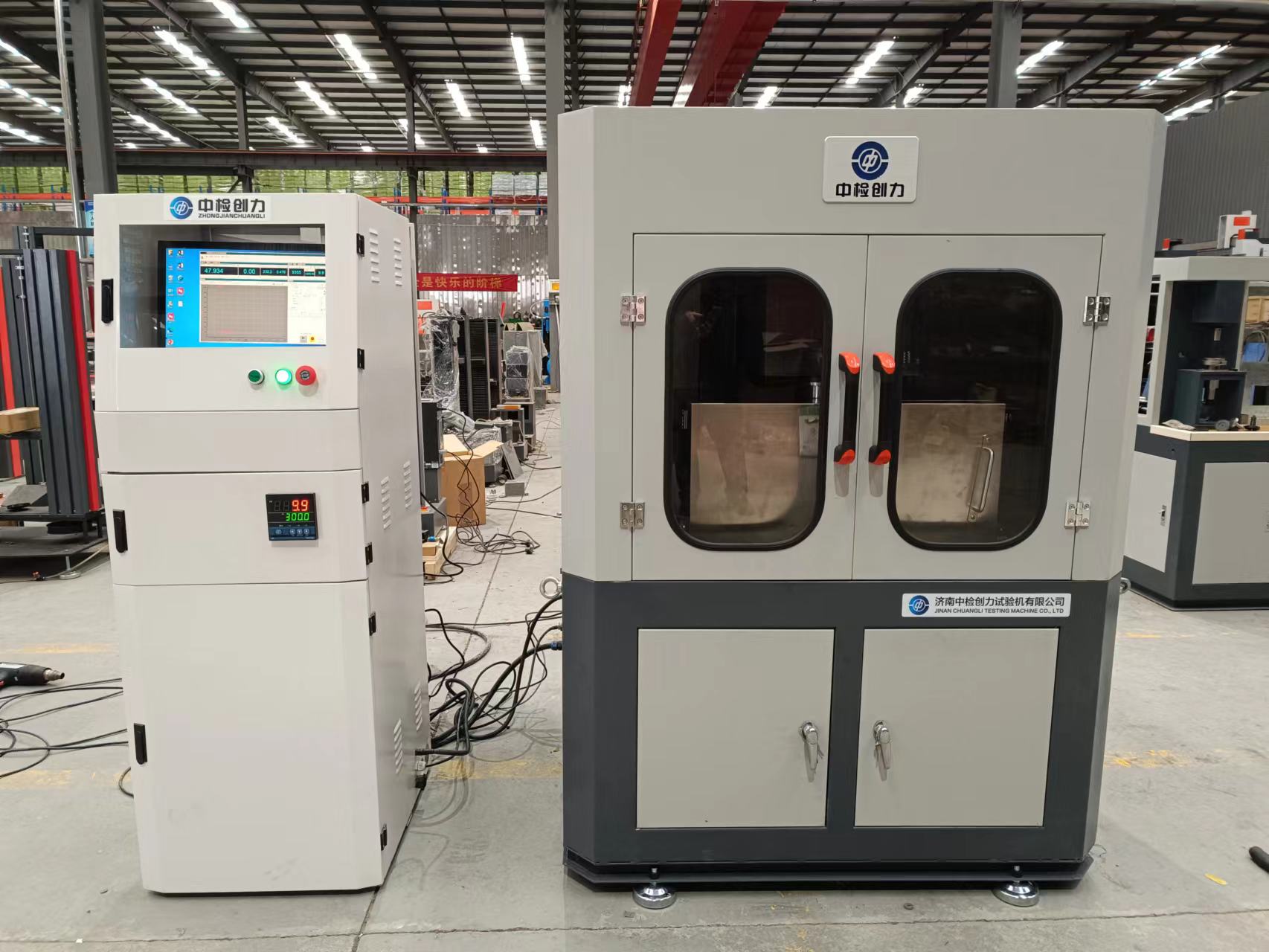
高温摩擦磨损
试验机通过模拟材料在高温条件下的摩擦接触状态,来评估材料的耐磨性能。其核心部件包括加载系统、加热系统、摩擦副和测量系统等。加载系统可以对试样施加精确的压力,使摩擦副之间产生符合实验要求的接触应力。加热系统能够将试样和摩擦环境加热到设定的高温范围,从几百摄氏度到上千摄氏度不等,以模拟如航空发动机叶片与机匣之间、冶金工业中高温轧辊与钢带之间等实际工况下的高温环境。在实验过程中,两个摩擦副在一定的相对运动速度下相互摩擦,测量系统则实时监测和记录摩擦系数、磨损量、温度变化等关键参数。这些数据对于分析材料在高温摩擦过程中的行为和性能变化规律有着重要意义。
高温摩擦磨损试验机的加热方式多种多样,常见的有电阻加热、感应加热和辐射加热等。电阻加热是通过在试样周围设置加热元件,利用电流通过电阻产生热量的原理,这种方式加热效率较高,温度控制相对容易,但可能存在加热不均匀的问题。感应加热则是利用交变磁场在试样中产生感应电流,进而使试样自身发热,它能够实现快速加热且加热深度较均匀,但设备成本相对较高。辐射加热是通过高温辐射源向试样辐射热量,可用于模拟高温辐射环境下的摩擦磨损情况,不过对辐射源的能量控制和均匀性要求较高。
在高温环境下,润滑和密封问题变得极为复杂。传统的润滑剂在高温下可能会分解、失效,因此需要研发特殊的高温润滑剂,或者采用自润滑材料。同时,为了防止高温环境下的氧化和杂质进入摩擦区域,试验机的密封设计至关重要。采用耐高温、耐磨损的密封材料和先进的密封结构,如迷宫密封、石墨密封等,可以有效保证试验环境的稳定性和准确性。
精确的测量和控制系统是高温摩擦磨损试验机的关键。摩擦系数的测量通常采用力传感器,通过测量摩擦力和正压力来计算摩擦系数。磨损量的测量方法包括称重法、轮廓仪测量法等,称重法简单直接,但对于微小磨损量的测量精度有限,轮廓仪测量法则可以更精确地测量磨损表面的形貌变化。控制系统需要精确控制加载力、转速、温度等参数,并且能够实现自动化的数据采集和处理,以保证试验结果的可靠性和重复性。
航空发动机在高温、高压、高速等极端工况下运行,其中的零部件如涡轮叶片、轴承等的摩擦磨损性能直接影响发动机的性能和寿命。高温摩擦磨损试验机可以模拟发动机内部的高温环境,研究新型高温合金、陶瓷基复合材料等在这种条件下的摩擦磨损特性,为航空发动机的材料选型和设计优化提供依据。
汽车发动机的活塞环与气缸壁、刹车盘与刹车片等部件在工作过程中也会面临高温摩擦问题。通过高温摩擦磨损试验,可以评估不同材料组合的耐磨性和摩擦性能,研发高性能的摩擦材料,提高汽车发动机的效率和刹车系统的可靠性,减少因摩擦磨损导致的故障和能量损失。
在冶金生产中,高温轧辊与轧材之间的摩擦磨损会影响轧材的表面质量和尺寸精度。利用高温摩擦磨损试验机,可以研究轧辊材料在高温轧制过程中的磨损机制,开发新型的耐磨轧辊材料,提高轧机的生产效率和产品质量。
在火力发电、核能发电等能源生产过程中,存在着大量高温摩擦部件,如汽轮机叶片、核反应堆中的控制棒驱动机构等。通过高温摩擦磨损试验,可以为这些关键部件的材料改进和维护提供数据支持,保障能源生产设备的安全稳定运行。
随着航空航天、能源等行业的发展,对材料在更高温度和压力下的摩擦磨损性能研究需求不断增加。未来的高温摩擦磨损试验机将朝着能够模拟更高极端条件的方向发展,例如能够实现 2000℃以上高温和更高压力的模拟。
借助先进的微观分析技术,如扫描电子显微镜(SEM)、原子力显微镜(AFM)等与试验机的联用,将能够更深入地研究材料在高温摩擦过程中的微观磨损机理,如材料的微观结构变化、表面化学反应等,从而为新型高性能材料的研发提供更准确的理论依据。
试验机将具备更智能的控制系统和数据处理能力,能够实现试验参数的自动优化、故障自动诊断和远程监控等功能。同时,与大数据和人工智能技术相结合,通过对大量试验数据的分析,预测材料在不同高温摩擦条件下的性能变化,提高试验效率和研究水平。
总之,高温摩擦磨损试验机在材料科学和工程领域中发挥着不可替代的作用,其不断发展和创新将为解决各行业中高温摩擦磨损问题提供更有力的技术支撑,推动相关产业向着更高性能、更可靠的方向发展。